TPS (Toyota Production System) принято считать универсальной, применимой к любой отрасли с небольшой адаптацией под конкретные условия. Однако внедрить ее в России и добиться существенных результатов пока удалось немногим. Например, заводу «КамАЗ», который за шесть лет с момента внедрения (2008 год) сократил издержки более чем на 30 млрд рублей. Или «Сбербанк», который за два года в четыре раза увеличил розничные продажи, сократив время ожидания в очередях на 36%.
Сложности при внедрении TPS в России
Несмотря на то, что в России единые подходы к внедрению бережливого производства поддерживаются приказом Минпромторга, существуют сложности внедрения TPS на предприятиях. Например, противоречивая терминология, сложности в финансово-экономическом состоянии предприятий, нехватка средств и ресурсов для преобразований и неприятие изменений сотрудниками компаний.
Многие российские предприятия, пытаясь улучшить производство, используют лишь несколько отдельных инструментов TPS, а не всю концепцию комплексного внедрения. Такой подход вряд ли приведет к ощутимым результатам.
Ситуация осложняется нехваткой опытных специалистов. Многочисленные самозваные «эксперты по бережливому производству», прочитав несколько книг по теме, берут на себя ответственность давать рекомендации по изменению бизнес-процессов, которых они не понимают. В результате внедрение срывается, эффект в лучшем случае не оказывается отрицательным, а руководители компаний приходят к убеждению, что «бережливое мышление» – обычное мошенничество. Я дважды сталкивался с последствиями работы таких «экспертов». Собственники компаний, заслышав от меня фразу «производственная система Toyota», начинали нехорошо улыбаться и быстро сворачивали разговор. Потом наводили обо мне справки у меня за спиной – не обманщик ли я. Причем в первом случае убедить человека, что в его же интересах вернуться к TPS, так и не удалось, несмотря на хорошие рекомендации от уважаемых им людей.
Кроме того, благодаря книгам и статьям о TPS, в которых пишут о резких улучшениях, многие российские производители рассчитывают на получение быстрых результатов от внедрения производственной системы в течение шести-восьми месяцев. Никому не хочется думать о том, что у Toyota на создание и отладку системы ушло несколько десятилетий. В реальности внедрение TPS в полном объеме займет несколько лет, хотя первый эффект проявится достаточно быстро. Когда опытные специалисты по бережливому производству, например, Джеймс Вумек и Дэниел Джонс, пишут, что что-то не так, если вы не получаете ощутимых результатов через две-три недели, речь идет об отдельных усовершенствованиях.
Ошибка 1: слепое копирование чужого успеха
Многие компании при внедрении TPS пытаются слепо копировать наработки в области процессов, в то время как в Toyota система является в первую очередь философией компании. Это скорее набор примеров, по которому можно опознать проблемы, актуальные для любой компании.
Принципы управления, описанные Джеффри Лайкером, также не универсальны. Классический список потерь Toyota и инструменты их устранения формировались на основе практической деятельности корпорации – для рынка автопрома. Поэтому, например, слепое следование созданию потока единичных изделий при организации производства в строительной компании может противоречить логике деятельности организации. Потому что при строительстве дома единичным изделием является квартира. Никто не будет строить дом поквартирно.
Приведу пример неудачной попытки слепого копирования TPS. В крупной строительной компании со штатом свыше тысячи сотрудников было принято решение о внедрении системы бережливого производства. Был привлечен специалист, который заставлял сотрудников учить наизусть принципы TPS, названия видов потерь и инструментов борьбы с ними. Во время обучения команда имитировала поток единичных изделий, решала абстрактные задачи, подгоняя реальные проблемы под потери из списков Toyota.
С момента внедрения «улучшений» эффективность работы компании снизилась на 18%. Ситуацию удалось спасти, изменив подход к внедрению. Во главу угла встали новые корпоративные принципы, 8, а не 14, которые были адаптированы под деятельность компании. Сотрудников просили не учить наизусть список потерь Toyota, а искать их самостоятельно на предприятии. Через полгода удельная прибыль на одного сотрудника выросла на 22-23%.
Ошибка 2: игнорирование потока создания ценности
Часто организации, начинающие внедрять у себя бережливое производство, сосредотачиваются на улучшении отдельных процессов, поток создания ценности «протекает» по ряду подразделений, для каждого отдельного потока назначается ответственный, но за поток в целом никто не отвечает. В такой ситуации части потока оптимизируются в отрыве от основного. Это значительно снижает эффективность усовершенствований и в ряде случаев может принести вред компании. Комплексного изменения не происходит, более того, может разрушиться уже возникший баланс между процессами.
Подразумевается, что результаты по отдельным процессам будут впоследствии объединены в карту создания ценности. Но при таком подходе удается получить лишь организационную схему предприятия, а не карту потока производимых продуктов. Это позволит оптимизировать штат, а не рабочие процессы и поток создания ценности.
Чтобы этого не произошло, необходимо назначить менеджера общего потока, который будет подчиняться руководителю, отвечать за внедрение бережливого производства, производить изменения в функциональных и структурных подразделениях, составлять, реализовывать и периодически корректировать план внедрения изменений, расставлять приоритеты, руководить разработкой карт потока и вести наблюдение за всеми сторонами внедрения.
При этом стоит помнить, что исключение потерь на уровне подразделений не менее важно, чем на уровне всего потока. Просто во втором случае эффект будет более масштабным, так как охватит предприятие в целом.
Ошибка 3: отсутствие вовлеченности персонала
Ключевые составляющие успеха TPS – люди и процессы. Главная роль у людей – именно они создают и поддерживают процессы и системы. Однако в России люди часто создают больше проблем, чем способствуют успеху внедрения. Ведь в большинстве компаний организационная структура вертикальная, в отличие от плоской у Toyota. Это создает необходимость сотрудникам подниматься на несколько уровней выше для решения и согласования вопросов, которые находятся в собственной компетенции. При этом обеспечивающие подразделения, отделы кадров, IT-службы, юристы, а также возложенные на производства контрольно-отчетные функции не всегда способствуют быстрому решению вопросов.
Важно, чтобы все сотрудники компании содействовали работе групп и помогали специалистам производственных подразделений, генерирующих добавленную стоимость. Для успешного внедрения при обучении должны разбираться проблемы, взятые из реальной трудовой жизни сотрудников и мешающие именно им работать более успешно. Желательно изучать мнения и настроения сотрудников, принимать меры по росту вовлеченности в процесс (убеждение, нематериальное стимулирование, главное – не принуждение), поощрять инициативу.
При формировании команд важно обеспечить взаимозаменяемость и взаимодополняемость сотрудников, потому что успех зависит не от отдельных людей, но от их совместных действий. Построение команды – достаточно серьезная задача, которая решается индивидуально в зависимости от культуры компании.
Будущее TPS в России
В России насчитывается несколько десятков предприятий, находящихся на различных этапах развития производственных систем и обладающих тем или иным опытом во внедрении. Это группы компаний «ГАЗ», «Иркут», «Русал», «Росатом» и ряд других.
Основываясь на личном опыте, я смело могу утверждать, что TPS может быть применена практически в любых организациях, независимо от формы собственности и отрасли. Главное – адаптировать ее под нужды компании, избегать ключевых ошибок и использовать накопленный российский опыт.
У тебя все классно, но, с моей точки зрения, ты не работаешь с фактом. Возможно, с фактом, внесенным вручную (типа информации о выполнении рабочей операции), ты так или иначе можешь работать. Но пока я от тебя ничего конкретного не слышал. Умалчиваешь по скромности или хранишь военную тайну супер-секретных технологий автоматизации сбора фактических данных с оборудования? Или вы уже с Диспетчером подружились? если нет - придется, скоро. Заставят "сверху". Цифра всех "оцифрует".
Сказал бы: "Да, блин - этого точно не хватает!" И я бы тебя понял.
Как это вообще возможно - построить расписание не зная состояние мощностей, количество и местонахождения ресурсов,..,?
Молодэц! Так откуда же ты получаешь информацию о нахождении, например, необходимой оснастки (если этот ресурс ограничен)? Откуда получаешь инфу, что станок встал на 5-10 минут из-за поломки? Откуда получаешь инфу о наработке, согласно которой нужно проводить плановый ТО и ППР? Все "ручками" в систему заносится? Это же все единое информационное пространство, сложное, многообразное, многофакторное и постоянно меняющееся.
Я тебе уже 100 раз говорил - откуда это информация заносится в систему планирования - не мое дело (в самой системе есть возможность ручного ввода и сканирования штрихкода - это стандартная возможность визуальных компонентов).
Основная рекомендация по сбору факта и событий - интеграция с ОПС серверами через сервер обмена сообщениями - типа ZeroMQ, RabbitMQ и т.д.
Главное в том, что система реагирует на эти сообщени в онлайне.
Тут кроме факта много чего есть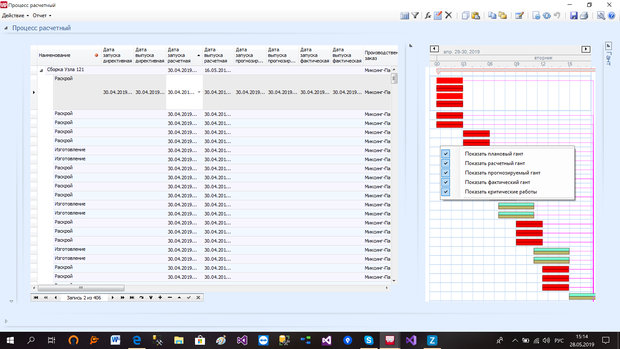
Понятие Массовое производство из ещё советского Госта до сих пор живёт "там", где имеет смысл. Для эпохи Альфреда Слоуна ~ 1965 год оно имело большой смысл. Но в зарубежной классификации есть такое понятие - поточное производство - его принципы и использовал Генри Форд.
Можно поискать информацию, что Поточное производство используется и в единичном производство, где на потоке производятся конструктивно подобные виды продукции или унифицированные детали.
Для TPS больший смысл имеет понятие "Производственная система".
На вашем форуме MES была длинная, длинная дискуссия на 121 страницу - активная часть с 2007 по 2014 год с названием "Бережливое производство" LM (Lean Manufacturing). Основной главной "мелодией" была тема, что Канбан не годится для мелкосерийного производства. Т.е доказать массовое производство на заводах Toyota было для участников дискуссии принципиальным вопросом?
Там вот это высказывание выразило важность вопроса для участников дискуссии для сравнения с MES:
Цитата из дискуссии на форуме MES- 2008 11:38 am "Ведь JIT, TPS - родились именно на массовом производстве, на Тойоте".
Так что же решили в конце? - не смог дочитать до конца все 121 страниц )))
Друзья, мое мнение, в тему комментариев (определение из экономического словаря):
МАССОВОЕ ПРОИЗВОДСТВО
Мне бы тоже хотелось что-то то сделать для Тойоты ))) , но не знаю точно как у них работает конвейер ...
Здесь ещё может мешать предвзятость, как на вашем форуме. Посмотрите - Канбан используется для тонкой настройки, и кроме него в TPS используется автоматизированная система планирования. И вам это будет интересно, т.к. касается составления расписаний + чего-то ещё ))) :
На рабочее место в нужный момент могут доставить всё что угодно. - Например, если это сварочный аппарат, то его привезут вовремя ))).
Один ваш коллега пишет по поводу расписаний в той дискуссии, и мне интересно ваше мнение:
Цитата из дискуссии на форуме MES: "А порядок работ никакая LM Вам не даст. Хейдзунка - всего лишь пожелание, один из эвристических принципов выравнивания нагрузки при составлении расписания работы в системе планирования вытягивающего типа под названием Канбан. Которая не работает в мелкосерийном производстве".
в тему самой статьи... ошибка во внедрении - это само внедрение.
Примерно как в Православную страну внедрять мусульманство. Очень сложно "мирным" путем переключить голову, только выселив одних и поселив других. Если вы не хотите заниматься переселением, нужно думать о том, как трансформировать или изменить мышление.
Поточное производство по ГОСТ 14.004-83 п. 29: Производство, характеризуемое расположением средств технологического оснащения в последовательности выполнения операций технологического процесса и определенным интервалом выпуска изделий.
В советское время работало много талантливых людей, и идёт только деградация, в т.ч. из-за недостатков образовательной системы.
Цитата из ещё советских источников!!! ))) :